The importance of treating water prior to the boiler process cannot be underestimated. Removal of organics, suspended particles, dissolved minerals, and dissolved gases is critical to avoid scaling and fouling, damaging and reducing the longevity of the expensive boiler/turbine process.
Boiler Feedwater Quality Recommendations
Boiler feedwater quality recommendations are stated by two groups - American Boiler Manufacturers Association (AMBA) and the more comprehensive American Society of Mechanical Engineers International Boiler and Pressure Vessel Code (ASME). These groups provide guidance and rules regarding safety for design, fabrication, and inspection of boilers and pressure vessels, as well as nuclear power plant components.
In general, the higher the operating drum pressure, the better the quality of boiler feedwater that must be provided to the steam generation equipment.
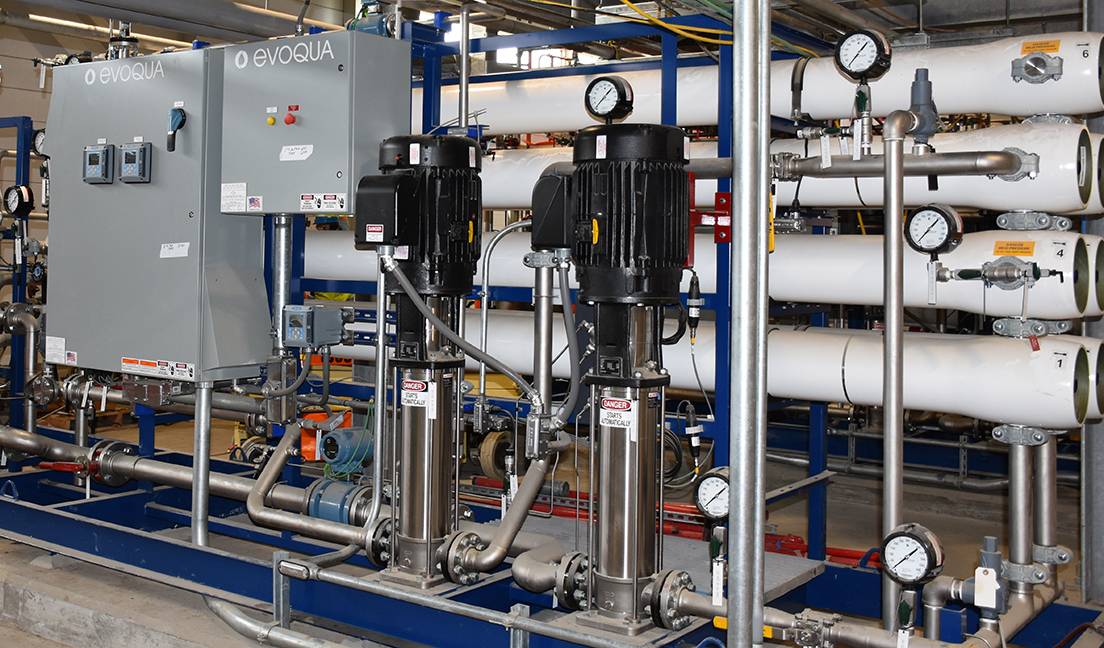
Feedwater Treatment Options
The most common treatment design consists of pretreatment filtration and chemical addition for removal of particulate matter and conditioning of the water chemistry. This is followed by a membrane process for the bulk reduction of dissolved minerals and a final polishing ion exchange step.
There is a clear trade-off between investment in water treatment equipment and water treatment chemicals. Often, investing in equipment that produces a higher quality boiler feedwater will significantly reduce chemical usage and increase the cycles of concentration, improving overall plant efficiency.
Evoqua will evaluate your specific feedwater quality, final water quality, and space requirements and apply our vast process knowledge to design a cost effective, service-friendly system that operates in an efficient manner. Offering you the best long-term solution is our goal.
Objectives of Boiler Feedwater Treatment:
- Reduce suspended solids and other particulate matter: The feedwater must be filtered to remove suspended solids. Dirt and particles can foul downstream processes such as reverse osmosis equipment and can accumulate as added sludge in the system. This treatment may include gross-screening (if drawn from a river source), clarification, media filtration, cartridge/bag filtration, microfiltration, and/or ultrafiltration.
- Condition the feedwater chemistry: The feedwater will most likely require chemical addition to reduce scaling or oxidation potential in the downstream processes and/or to reduce CO2. This is usually accomplished with antiscalant, a reducing agent such as sodium bisulfite, acid and/or caustic.
- Bulk reduction of suspended solids and organics: Under most conditions it is cost effective to use reverse osmosis technology to remove the majority of dissolve minerals (either defined as conductivity or total dissolve solids) and organic constituents prior to final polishing to boiler and turbine manufacturer quality requirements. Reverse osmosis membranes remove up to 99% of dissolve minerals and are an excellent barrier for the reduction of small, medium and large-chain organics. In some cases, it may be cost effective to include a second reverse osmosis step, or second pass, to further process the water prior to polishing.
- Degasification: While most plant designs rely on the reduction of gases in the steam cycle by introducing high-quality boiler feedwater to the condenser at vacuum followed by an oxygen scavenger, there are conditions where CO2 and O2 reduction are desired. This can be accomplished by a membrane process, wherein a sweep gas (usually nitrogen) pulls oxygen from the water under vacuum, or via a vacuum tower with special packing that causes the gases to separate from the water and be extracted.
- Final polishing: Boiler and turbine water quality requirements are stringent. It is critical to achieve low conductivity, silica, sodium and often total organic carbon (TOC) in the final treated water. This polishing step can consist of traditional ion exchange (either off-site regenerated service DI, which minimizes waste and chemical handling issues, or in-situ regenerated equipment) or continuous electronic deionization processes (CEDI) that use a resin-based membrane process and electrical current to remove trace dissolved minerals.
- Other processes: In some cases, carbon may be used as pretreatment and UV may be incorporated in the polishing step to further reduce organics.
- Reliable uptime operation: The boiler feedwater treatment plant must be both reliable and available a very high amount of the time, or the plant may be forced to reduce its operation at significant cost to the owner. Properly designed equipment, redundant design and remote monitoring technologies may be employed, based on each project need, to achieve those goals.